AspectDetailsAffordabilityWarehouse rental in Karachi offers cost-effective options compared to owning a warehouse. Businesses can save…
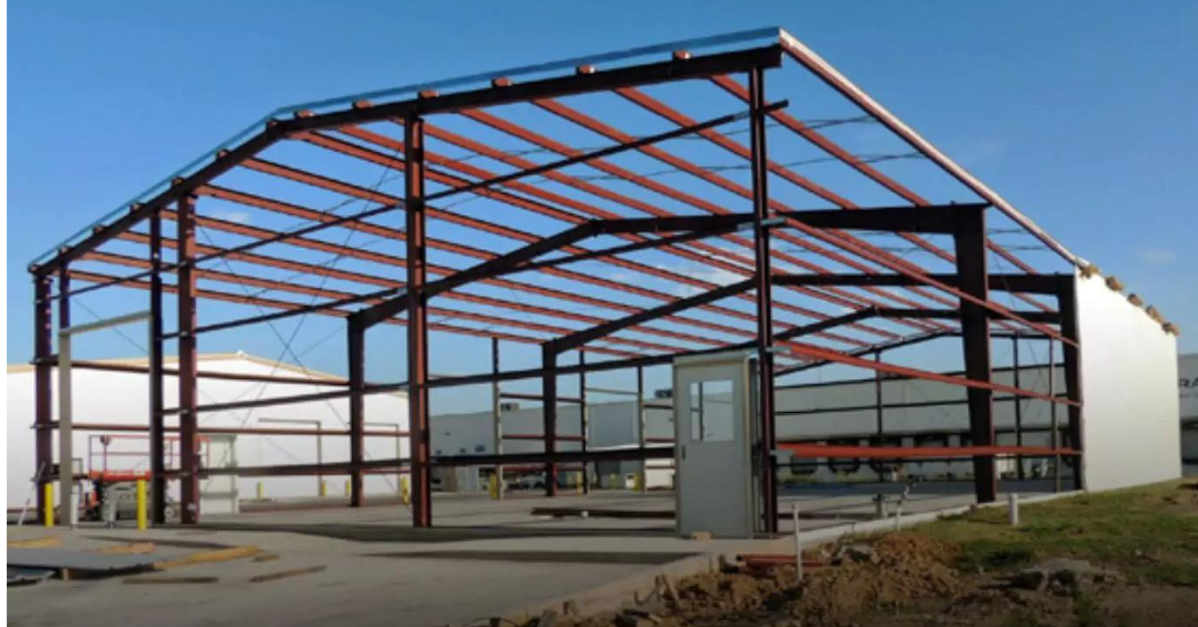
EPACK Step-by-Step Guide to Constructing a Pre-Engineered Building in Karachi
- Introduction
- Importance of pre-engineered buildings (PEBs) in urban construction
- Overview of the construction process
- Preparation Phase
- Site selection and evaluation
- Permits and regulatory approvals
- Design and Engineering
- Conceptual design phase
- Detailed engineering and customization options
- Procurement of Materials
- Ordering PEB components
- Quality assurance and delivery logistics
- Foundation and Site Preparation
- Excavation and leveling
- Foundation construction and reinforcement
- PEB Installation
- Erection of main frames and secondary members
- Roof and wall panel installation
- Utilities and Infrastructure
- Electrical and plumbing installations
- HVAC systems and insulation
- Interior Finishes
- Flooring, partitions, and interior fittings
- Safety and accessibility considerations
- Testing and Commissioning
- Structural integrity tests
- Quality checks and final inspections
- Handover and Maintenance
- Client walkthrough and documentation
- Ongoing maintenance and warranty support
- Conclusion
- Summary of the PEB construction process
- Recommendations for future projects
Article:
EPACK Step-by-Step Guide to Constructing a Pre-Engineered Building in Karachi
Constructing a pre-engineered building (PEB) in Karachi involves a systematic approach that combines efficient design, quality materials, and precise construction techniques. This step-by-step guide outlines the essential phases and considerations for successfully completing a PEB project in Pakistan’s vibrant metropolis.
Introduction
Pre-engineered buildings (PEBs) have gained popularity in Karachi’s construction industry due to their rapid assembly, cost-effectiveness, and structural durability. Whether for commercial complexes, industrial warehouses, or residential developments, PEBs offer streamlined solutions tailored to urban environments.
Preparation Phase
Before commencing construction, thorough site evaluation and selection are critical. Factors such as accessibility, soil conditions, and zoning regulations impact site suitability. Securing necessary permits and regulatory approvals ensures compliance with local building codes and safety standards.
Design and Engineering
The design phase begins with conceptual sketches and evolves into detailed engineering plans. PEBs allow for customization in structural layout, architectural finishes, and functional requirements. Collaborating with experienced architects and engineers ensures design feasibility and optimizes project outcomes.
Procurement of Materials
Procuring PEB components involves ordering structural frames, roof panels, wall cladding, and insulation materials from reputable suppliers. Rigorous quality assurance processes during manufacturing and efficient delivery logistics are essential to maintain project timelines.
Foundation and Site Preparation
Site preparation begins with excavation and leveling to create a stable foundation. Constructing reinforced concrete foundations ensures structural stability and load-bearing capacity, critical for supporting the PEB’s framework and operational requirements.
PEB Installation
Erecting the PEB involves assembling primary frames, secondary members, and connecting components according to engineered drawings. Roof and wall panels are installed to enclose the structure, providing weatherproofing and thermal insulation properties.
Utilities and Infrastructure
Integrating electrical, plumbing, and HVAC systems enhances building functionality and occupant comfort. Installing insulation materials within wall cavities and roofing systems improves energy efficiency, mitigates heat transfer, and reduces operational costs.
Interior Finishes
Interior finishes encompass flooring installations, partitioning walls, and fitting fixtures that align with aesthetic preferences and functional needs. Emphasizing safety features, such as fire-resistant materials and accessible design elements, ensures compliance with building regulations.
Testing and Commissioning
Conducting structural integrity tests and quality checks verifies compliance with design specifications and safety standards. Final inspections certify operational readiness and identify any deficiencies requiring rectification before project handover.
Handover and Maintenance
Client walkthroughs facilitate project handover, documenting completed works and operational manuals. Establishing proactive maintenance schedules and providing warranty support prolongs building lifespan and sustains performance efficiencies.
Conclusion
Navigating the construction of a pre-engineered building (PEB) in Karachi demands meticulous planning, technical expertise, and adherence to regulatory requirements. By following this step-by-step guide, stakeholders can achieve successful project outcomes and contribute to Karachi’s dynamic urban landscape.
FAQs
- How long does it take to construct a pre-engineered building in Karachi?
- Construction timelines vary based on project complexity and size. Typically, PEBs can be erected faster than traditional buildings due to standardized components and assembly processes.
- Are pre-engineered buildings suitable for seismic zones like Karachi?
- Yes, PEBs can be engineered to withstand seismic activities with appropriate structural design and reinforcement.
- What are the cost benefits of choosing a pre-engineered building over traditional construction methods?
- PEBs often result in lower construction costs due to reduced labor, faster assembly times, and minimal material waste.
- Do pre-engineered buildings require specialized maintenance after construction?
- Routine maintenance is recommended to ensure optimal performance and longevity. PEBs generally require less maintenance compared to traditional structures.
- Can PEBs be customized to meet specific architectural requirements in Karachi?
- Yes, PEBs offer design flexibility and can be customized to accommodate various architectural styles and functional needs.
This Post Has 0 Comments