FeatureDescriptionStrategic LocationKarachi's top warehouses are strategically located near key transportation hubs such as the Karachi…
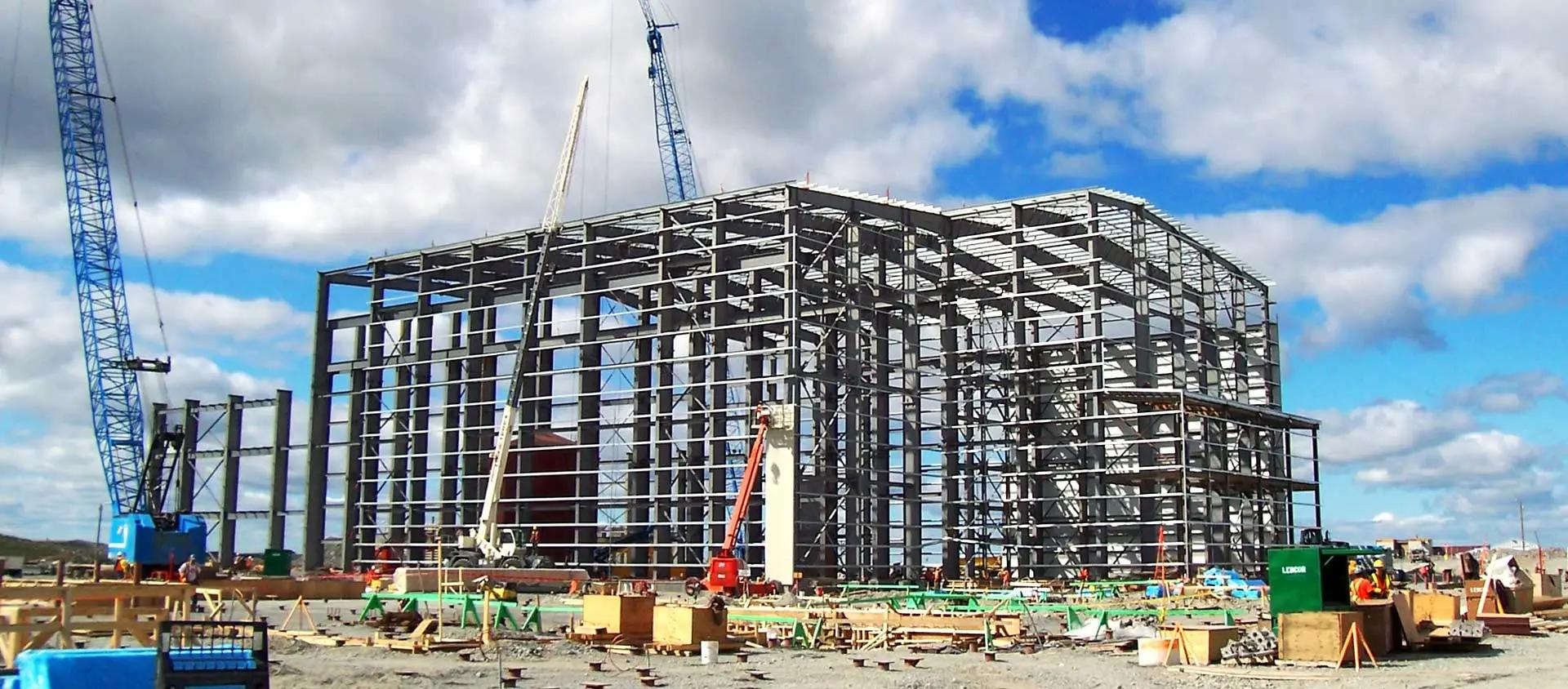
ACCO Comparing Pre Engineering vs. Traditional Construction in Pakistan
- Introduction
- Brief Overview of Construction Methods in Pakistan
- Importance of Construction Methodology
- Understanding Pre-Engineering Construction
- Definition and Concept
- Key Features of Pre-Engineering Construction
- Understanding Traditional Construction
- Definition and Concept
- Key Features of Traditional Construction
- Comparative Analysis of Pre-Engineering and Traditional Construction
- Cost Efficiency
- Time Efficiency
- Material Usage
- Labor Requirements
- Cost Efficiency
- Initial Costs
- Long-Term Savings
- Time Efficiency
- Construction Speed
- Project Deadlines
- Material Usage
- Sustainability
- Waste Management
- Labor Requirements
- Skill Levels
- Labor Availability
- Structural Integrity and Safety
- Durability
- Safety Standards
- Environmental Impact
- Carbon Footprint
- Waste Generation
- Aesthetic Flexibility
- Design Options
- Customization
- Case Studies in Pakistan
- Successful Pre-Engineering Projects
- Successful Traditional Construction Projects
- Challenges and Limitations
- Pre-Engineering Challenges
- Traditional Construction Challenges
- Future Trends in Pakistani Construction
- Emerging Technologies
- Industry Predictions
- Conclusion
- Summary of Key Points
- Final Thoughts on Pre-Engineering vs. Traditional Construction
- FAQs
- What is the main difference between pre-engineering and traditional construction?
- How does pre-engineering contribute to cost savings?
- Are pre-engineered buildings as durable as traditional ones?
- What are the environmental benefits of pre-engineering construction?
- Is traditional construction becoming obsolete?
Article
Introduction
When it comes to building infrastructure, the choice between pre-engineering and traditional construction methods can significantly impact the project’s outcome. In Pakistan, this decision is increasingly vital as the construction industry continues to grow. Understanding these two distinct approaches and their implications can help builders, developers, and stakeholders make informed decisions.
Understanding Pre-Engineering Construction
Pre-engineering construction, often referred to as pre-engineered buildings (PEBs), involves designing and fabricating building components in a factory before assembling them on-site. This method is characterized by its efficiency, precision, and flexibility.
Key Features of Pre-Engineering Construction
Pre-engineered construction boasts several notable features:
- Modular Design: Components are manufactured in standardized modules.
- Quick Assembly: On-site construction time is significantly reduced.
- Precision: Factory fabrication ensures high accuracy.
- Cost-Effective: Optimized material use reduces overall costs.
Understanding Traditional Construction
Traditional construction, on the other hand, involves building structures on-site from the ground up using standard construction methods. This approach has been the cornerstone of construction practices for centuries.
Key Features of Traditional Construction
Traditional construction features include:
- Custom Design: Tailored to specific site and client needs.
- Material Versatility: Wide range of materials can be used.
- On-Site Fabrication: Components are crafted and assembled on-site.
- Labor-Intensive: Requires a significant workforce.
Comparative Analysis of Pre-Engineering and Traditional Construction
Cost Efficiency
Initial Costs
Pre-engineered buildings often have higher initial costs due to factory manufacturing. However, these costs are offset by savings in labor and time.
Long-Term Savings
Pre-engineering reduces maintenance costs and energy consumption, leading to long-term financial benefits.
Time Efficiency
Construction Speed
Pre-engineering dramatically shortens construction time, with some projects completed in weeks rather than months.
Project Deadlines
Meeting project deadlines is more predictable with pre-engineered methods, minimizing delays and associated costs.
Material Usage
Sustainability
Pre-engineered buildings use materials more efficiently, reducing waste and promoting sustainability.
Waste Management
Factory-controlled environments ensure minimal material waste compared to on-site construction.
Labor Requirements
Skill Levels
Pre-engineered construction requires fewer skilled workers on-site, relying more on factory-based precision.
Labor Availability
Traditional construction demands a larger, often less specialized workforce, which can be challenging to manage.
Structural Integrity and Safety
Durability
Both methods can produce durable buildings, but pre-engineered structures benefit from controlled manufacturing conditions.
Safety Standards
Pre-engineered buildings adhere to stringent safety standards, reducing risks during construction.
Environmental Impact
Carbon Footprint
Pre-engineered buildings typically have a lower carbon footprint due to efficient material use and reduced transportation needs.
Waste Generation
Less on-site waste is generated with pre-engineered construction, contributing to a cleaner environment.
Aesthetic Flexibility
Design Options
Traditional construction offers more flexibility in design and materials, catering to unique aesthetic preferences.
Customization
Pre-engineered buildings can be customized to some extent, but they may lack the same level of artistic freedom as traditional methods.
Case Studies in Pakistan
Successful Pre-Engineering Projects
Examples include industrial warehouses and commercial complexes that highlight the efficiency and speed of pre-engineered construction.
Successful Traditional Construction Projects
Historical buildings and residential areas showcase the enduring appeal and customization possibilities of traditional construction.
Challenges and Limitations
Pre-Engineering Challenges
- Limited design flexibility
- Higher initial costs
- Dependence on precise manufacturing
Traditional Construction Challenges
- Longer construction time
- Higher labor costs
- Greater environmental impact
Future Trends in Pakistani Construction
Emerging Technologies
Integration of smart technologies and sustainable materials is reshaping both pre-engineering and traditional construction methods.
Industry Predictions
The trend towards pre-engineered buildings is expected to grow, driven by the need for efficient, cost-effective construction solutions.
Conclusion
Both pre-engineering and traditional construction methods have their merits and drawbacks. Pre-engineered buildings offer efficiency, precision, and cost savings, while traditional construction provides flexibility and a rich legacy of craftsmanship. In Pakistan, the choice between these methods will depend on specific project requirements, budget constraints, and aesthetic preferences.
FAQs
What is the main difference between pre-engineering and traditional construction?
Pre-engineering involves factory-fabricated components assembled on-site, whereas traditional construction builds structures entirely on-site.
How does pre-engineering contribute to cost savings?
Pre-engineering reduces labor and material costs through efficient use and quick assembly, resulting in long-term savings.
Are pre-engineered buildings as durable as traditional ones?
Yes, pre-engineered buildings can be as durable as traditional structures, often benefiting from controlled manufacturing environments.
What are the environmental benefits of pre-engineering construction?
Pre-engineering reduces material waste and lowers the carbon footprint due to efficient resource use and minimized transportation needs.
Is traditional construction becoming obsolete?
Not necessarily. While pre-engineering is growing in popularity, traditional construction remains relevant for projects requiring high customization and unique designs.
This Post Has 0 Comments