AspectDetailsAffordabilityWarehouse rental in Karachi offers cost-effective options compared to owning a warehouse. Businesses can save…
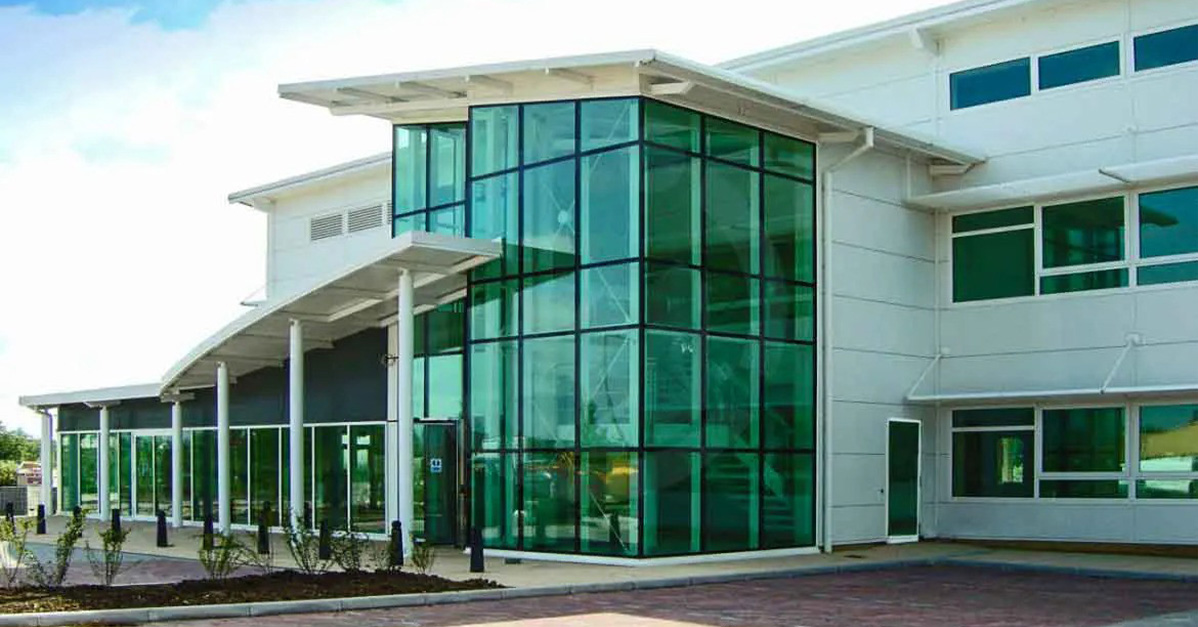
Successful Implementation of PEBs in Commercial Construction Projects in Pakistan
Introduction: Commercial construction projects in Pakistan face unique challenges, including tight deadlines, budget constraints, and the need for innovative solutions to meet diverse requirements. Pre-engineered buildings (PEBs) have emerged as a preferred choice for commercial developments, offering unparalleled efficiency, flexibility, and cost-effectiveness. In this case study, we explore the successful implementation of PEBs in commercial construction projects in Pakistan, highlighting key factors that contributed to their success and lessons learned along the way.
Project Overview: The commercial construction project under review is a large-scale retail complex located in a bustling urban center in Pakistan. The project aimed to create a modern, functional, and visually appealing retail space to accommodate various businesses, including shops, restaurants, and entertainment venues. With a tight construction schedule and budgetary constraints, the project required a construction solution that could deliver high-quality results within a short timeframe and cost-effective manner.
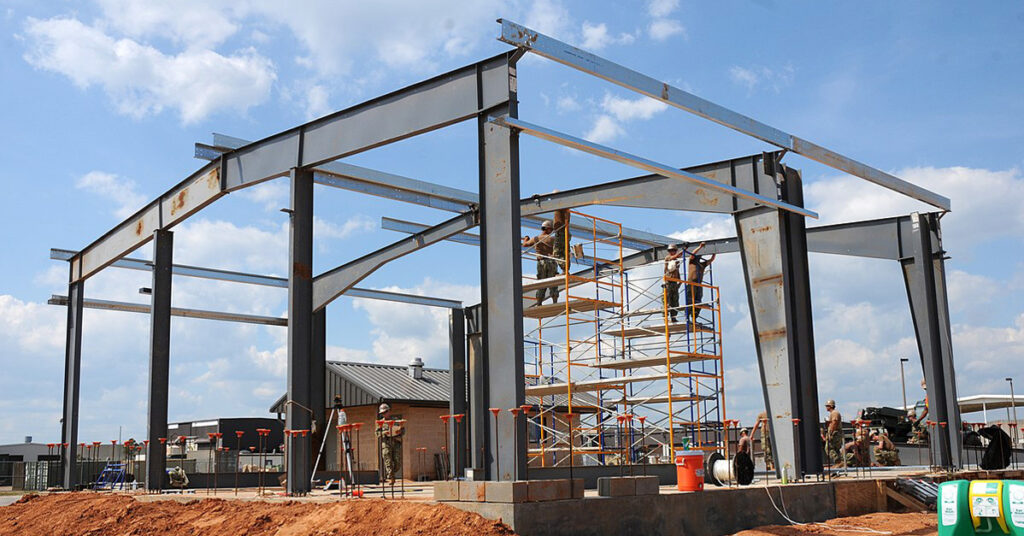
Challenges Faced: Several challenges were encountered during the planning and execution phases of the commercial construction project, including:
- Tight Timelines: The project had stringent deadlines due to market demand and lease agreements with tenants, requiring rapid construction and timely completion.
- Budget Constraints: Cost management was a critical consideration, necessitating a construction solution that offered cost-effectiveness without compromising quality or design.
- Design Flexibility: The project required a flexible design to accommodate diverse tenant requirements, spatial configurations, and aesthetic preferences.
- Structural Integrity: Given the size and complexity of the retail complex, ensuring structural integrity and safety was paramount to meet regulatory requirements and ensure occupant safety.
Solution: Implementation of PEBs To address the challenges faced and achieve the project’s objectives, the decision was made to utilize Pre-Engineered Buildings (PEBs) for the construction of the retail complex. PEBs offered several advantages that aligned with the project’s requirements:
- Speed of Construction: PEBs can be manufactured off-site in a controlled environment while site preparation and foundation work are underway, allowing for faster construction and accelerated project timelines.
- Cost-Effectiveness: The efficient use of materials, streamlined construction process, and reduced labor requirements inherent to PEBs offered cost savings compared to conventional construction methods, helping to stay within budget constraints.
- Design Flexibility: PEBs provided the flexibility to customize the design according to tenant specifications, allowing for diverse spatial configurations, facade treatments, and interior layouts to create a unique and attractive retail environment.
- Structural Integrity: PEBs are engineered to meet stringent structural standards and safety regulations, ensuring the durability, stability, and safety of the retail complex for occupants and visitors.
Implementation Process: The implementation of PEBs in the commercial construction project involved several key steps:
- Design Collaboration: Close collaboration between architects, engineers, and PEB manufacturers facilitated the development of a tailored design that met the project’s functional, aesthetic, and structural requirements.
- Manufacturing and Fabrication: PEB components were manufactured off-site at specialized facilities using advanced technology and quality control measures to ensure precision, consistency, and adherence to project specifications.
- Site Preparation and Assembly: Concurrently with foundation work, PEB components were delivered to the construction site and assembled according to the approved design, leveraging prefabricated elements for efficient installation and assembly.
- Quality Assurance and Safety Compliance: Rigorous quality assurance checks and safety protocols were implemented throughout the construction process to maintain high standards of workmanship, compliance with regulations, and adherence to project timelines.
Results and Outcomes: The successful implementation of PEBs in the commercial construction project yielded several positive outcomes:
- Timely Completion: The use of PEBs enabled the project to meet tight deadlines, allowing for the timely opening of the retail complex and the commencement of business operations as scheduled.
- Cost Savings: PEB construction proved to be cost-effective, helping to optimize project budgets and allocate resources efficiently without compromising on quality or design.
- Design Flexibility: The flexibility of PEBs allowed for the realization of diverse tenant requirements and design preferences, resulting in a visually appealing and functional retail environment that attracted tenants and customers alike.
- Structural Integrity: The structural integrity and safety of the retail complex were ensured through the use of high-quality PEB components and adherence to engineering standards and regulatory requirements.
Lessons Learned: The successful implementation of PEBs in the commercial construction project provided valuable insights and lessons learned for future projects:
- Early Planning and Collaboration: Early engagement with PEB manufacturers and stakeholders facilitated collaborative decision-making and streamlined the design and implementation process.
- Detailed Design Specifications: Clear and detailed design specifications were essential to ensure that PEB components met project requirements and aligned with tenant expectations.
- Quality Control and Safety Measures: Rigorous quality control measures and safety protocols were instrumental in maintaining construction standards, minimizing risks, and ensuring project success.
- Continuous Communication: Open and transparent communication between project teams, contractors, and stakeholders fostered a culture of collaboration, accountability, and problem-solving throughout the construction process.
Conclusion: The successful implementation of Pre-Engineered Buildings (PEBs) in the commercial construction project exemplifies the benefits of leveraging innovative construction solutions to overcome challenges and achieve project objectives. By embracing PEBs, the project was able to meet tight deadlines, stay within budget constraints, accommodate diverse tenant requirements, and ensure structural integrity and safety. The lessons learned from this case study underscore the importance of early planning, collaboration, detailed design specifications, quality control, and continuous communication in the successful implementation of PEBs in commercial construction projects in Pakistan. As the construction industry continues to evolve, PEBs offer a sustainable, cost-effective, and efficient solution for meeting the growing demand for modern and functional commercial spaces in Pakistan’s dynamic urban landscape.
This Post Has 0 Comments