AspectDetailsAffordabilityWarehouse rental in Karachi offers cost-effective options compared to owning a warehouse. Businesses can save…
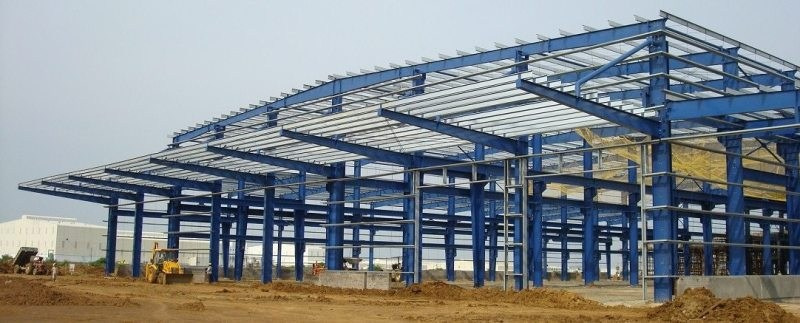
EPACK A Complete Guide to Prefabricated Multi-Story Buildings in Pakistan
Main Heading | Sub-Topics |
---|---|
Introduction to Prefabricated Multi-Story Buildings | Overview of prefabrication, growth of multi-story prefabrication, and relevance in Pakistan’s construction industry |
History of Prefabricated Construction | Origins of prefabricated buildings, evolution over the years, and key milestones in Pakistan |
Types of Prefabricated Multi-Story Buildings | Overview of different types, including modular, panelized, and hybrid prefabrication, and examples in Pakistan |
Benefits of Prefabricated Multi-Story Buildings | Detailed exploration of cost savings, speed of construction, sustainability, and safety |
Key Materials Used in Prefabrication | Analysis of commonly used materials like steel, concrete, and wood, and their advantages in multi-story prefabrication |
Design and Customization Options | Customization potential in prefabricated buildings, flexibility in architectural design, and meeting diverse needs in Pakistan |
Structural Integrity and Safety Considerations | Engineering principles behind strong prefabricated buildings, quality control, and safety compliance |
Seismic Resilience in Prefabricated Buildings | Importance of seismic design in Pakistan, engineering solutions, and examples of earthquake-resistant prefabricated buildings |
Sustainability and Environmental Impact | Eco-friendly aspects of prefabrication, waste reduction, energy efficiency, and contribution to green building practices in Pakistan |
Cost Considerations and Financial Benefits | In-depth cost analysis, upfront savings, long-term financial benefits, and comparison with traditional construction |
Timeline for Prefabricated Construction Projects | Phases of a prefabricated building project, from design to assembly, and typical timelines compared to traditional construction |
Innovative Technologies in Prefabrication | Role of advanced technologies like BIM, automation, and 3D printing in enhancing prefabrication processes |
Challenges in Prefabricated Construction in Pakistan | Common challenges, such as logistical, regulatory, and market acceptance issues, and strategies to overcome them |
Regulations and Building Codes | Overview of Pakistani building codes relevant to prefabrication, compliance requirements, and government incentives |
Case Studies: Successful Prefabricated Multi-Story Projects | Examples of successful multi-story prefabricated buildings in Pakistan, insights from these projects, and lessons learned |
Comparing Prefabrication to Traditional Construction | Detailed comparison in terms of cost, speed, quality, and environmental impact, and when to choose prefabrication |
Future Trends in Prefabricated Construction in Pakistan | Emerging trends, potential growth areas, and the future outlook for prefabrication in the country |
How to Choose the Right Prefabrication Partner | Criteria for selecting a prefabrication partner, evaluating experience, technological capabilities, and project portfolio |
Steps to Planning a Prefabricated Multi-Story Building Project | Step-by-step guide to planning a project, from initial concept to completion, and key considerations for success |
FAQs on Prefabricated Multi-Story Buildings in Pakistan | Addressing common questions about prefabricated multi-story buildings, including cost, timelines, safety, and customization options |
Conclusion: The Growing Role of Prefabrication in Pakistan | Summary of the key points, the benefits of adopting prefabrication, and the potential impact on Pakistan’s construction industry |
A Complete Guide to Prefabricated Multi-Story Buildings in Pakistan
SEO Meta-Description: Explore the complete guide to prefabricated multi-story buildings in Pakistan, covering everything from benefits and materials to design options and cost considerations.
Introduction to Prefabricated Multi-Story Buildings
In recent years, prefabricated multi-story buildings have emerged as a revolutionary solution to meet the growing demand for residential, commercial, and industrial spaces in Pakistan. Prefabrication, the process of manufacturing building components in a controlled factory environment and then assembling them on-site, offers a range of benefits that are transforming the construction industry. This guide provides a comprehensive overview of prefabricated multi-story buildings, highlighting their advantages, design possibilities, and the factors driving their adoption in Pakistan.
History of Prefabricated Construction
The concept of prefabricated construction dates back centuries, with early examples found in ancient civilizations that used modular components for building structures. However, it was during the industrial revolution that prefabrication gained significant traction, particularly in Europe and North America. The post-World War II era saw a surge in prefabricated housing as countries sought quick and cost-effective solutions to rebuild cities. In Pakistan, the adoption of prefabricated construction began more recently, with the technology evolving to meet the country’s unique needs. Today, prefabrication is increasingly recognized for its potential to address the challenges of rapid urbanization and infrastructure development in Pakistan.
Types of Prefabricated Multi-Story Buildings
Prefabricated multi-story buildings come in various forms, each offering distinct advantages depending on the project’s requirements. The three primary types of prefabricated buildings are:
- Modular Prefabrication: Involves creating entire rooms or sections of a building in a factory setting. These modules are then transported to the site and assembled, offering quick construction times and high quality.
- Panelized Prefabrication: Consists of building large panels, such as walls and floors, in a factory. These panels are then assembled on-site to create the structure. This method allows for greater flexibility in design.
- Hybrid Prefabrication: Combines elements of both modular and panelized prefabrication, offering a balance between speed, customization, and cost.
In Pakistan, all three types are used depending on the specific needs of the project, from residential apartments to commercial office spaces.
Benefits of Prefabricated Multi-Story Buildings
Prefabricated multi-story buildings offer numerous benefits that make them an attractive option for construction in Pakistan:
- Cost Savings: Prefabrication reduces material waste, labor costs, and construction time, leading to significant cost savings. The controlled factory environment ensures that materials are used efficiently, and the assembly process is faster than traditional construction methods.
- Speed of Construction: Prefabricated buildings can be completed in a fraction of the time required for traditional construction. This speed is particularly beneficial in Pakistan, where rapid urbanization demands quick solutions to housing and infrastructure needs.
- Sustainability: Prefabricated buildings are environmentally friendly, using sustainable materials and generating less waste. The energy efficiency of these buildings also contributes to reduced operational costs and a lower carbon footprint.
- Safety: The factory-controlled environment of prefabrication allows for rigorous quality control, resulting in buildings that meet high safety standards. Additionally, on-site construction risks are minimized due to the reduced need for extensive on-site work.
Key Materials Used in Prefabrication
The materials used in prefabricated multi-story buildings are chosen for their strength, durability, and environmental impact. Common materials include:
- Steel: Known for its strength and flexibility, steel is a popular choice for the structural framework of prefabricated buildings. It is particularly suitable for multi-story construction due to its load-bearing capacity.
- Concrete: Precast concrete panels are widely used for walls, floors, and foundations. Concrete offers excellent fire resistance, thermal mass, and durability, making it ideal for prefabricated buildings in Pakistan.
- Wood: While less common in multi-story buildings, wood is used in certain applications, particularly for interior finishes and lightweight structures. Engineered wood products offer strength and stability while providing a sustainable option.
These materials are selected based on the specific needs of the project, ensuring that the final building meets the required standards for safety, durability, and environmental performance.
Design and Customization Options
One of the misconceptions about prefabricated buildings is that they offer limited design options. In reality, modern prefabrication techniques allow for a high degree of customization and architectural innovation. Architects and designers can work with prefabrication companies to create unique layouts and facades that meet specific project requirements. In Pakistan, where cultural and aesthetic preferences vary widely, the ability to customize prefabricated buildings to suit these needs is a significant advantage. From modern office buildings to traditional-style residential complexes, prefabrication can accommodate a wide range of design possibilities.
Structural Integrity and Safety Considerations
Structural integrity is a critical consideration in the construction of multi-story buildings, and prefabrication excels in this area. The components used in prefabricated buildings are manufactured under strict quality control conditions, ensuring that they meet or exceed industry standards for strength and durability. In addition, the assembly process is designed to enhance the overall structural integrity of the building, with connections and joints engineered to provide maximum stability. In Pakistan, where seismic activity is a concern, the robust engineering of prefabricated buildings offers an added layer of safety, making them a reliable choice for multi-story construction.
Seismic Resilience in Prefabricated Buildings
Given Pakistan’s location in a seismically active region, the ability of buildings to withstand earthquakes is of paramount importance. Prefabricated multi-story buildings are designed with seismic resilience in mind, using advanced engineering techniques to ensure they can absorb and dissipate seismic energy. The precision manufacturing of components allows for better integration and connection of structural elements, which is critical in resisting earthquake forces. Real-world examples from earthquake-prone regions demonstrate that prefabricated buildings can perform exceptionally well during seismic events, providing a safer environment for occupants.
Sustainability and Environmental Impact
Sustainability is a key advantage of prefabricated construction. The factory-controlled environment of prefabrication minimizes waste by using materials more efficiently and reducing on-site construction debris. Additionally, many prefabricated buildings incorporate sustainable materials, such as recycled steel and low-emission concrete, further reducing their environmental impact. The energy efficiency of prefabricated buildings also contributes to sustainability, as they require less energy for heating and cooling due to better insulation and airtight construction. In Pakistan, where environmental concerns are becoming increasingly important, prefabrication offers a way to construct buildings that are not only cost-effective but also environmentally responsible.
Cost Considerations and Financial Benefits
Cost is a major factor driving the adoption of prefabricated multi-story buildings in Pakistan. The financial benefits of prefabrication are realized through several key factors:
- Upfront Savings: The ability to manufacture building components in bulk leads to significant savings on materials. Additionally, the reduced labor costs associated with prefabrication contribute to lower overall project expenses.
- Long-Term Benefits: Prefabricated buildings often have lower maintenance costs due to the high quality of materials and construction. The energy efficiency of these buildings also results in lower utility bills over time.
- Comparison with Traditional Construction: When compared to traditional construction methods, prefabrication offers more predictable costs and fewer budget overruns. The reduced likelihood of delays further enhances the financial appeal of prefabricated buildings.
Timeline for Prefabricated Construction Projects
The timeline for constructing a prefabricated multi-story building is significantly shorter than that of a traditional building. The process can be broken down into several phases:
- Design and Planning: This initial phase involves working with architects and engineers to create detailed plans for the building. The use of technologies like Building Information Modeling (BIM) can streamline this process, ensuring that all aspects of the project are carefully coordinated.
- Manufacturing: Once the design is finalized, the building components are manufactured in a factory setting. This phase is typically much faster than on-site construction, as it is not subject to weather delays or other common issues.
- Transportation and Assembly: The final phase involves transporting the prefabricated components to the construction site and assembling them. This phase is also quicker than traditional construction, as the components are designed to fit together precisely, reducing the need for extensive on-site adjustments.
In total, a prefabricated multi-story building can be completed in a fraction of the time required for a traditionally constructed building, making it an ideal solution for projects with tight deadlines.
Innovative Technologies in Prefabrication
The success of prefabricated multi-story buildings is closely tied to the use of innovative technologies. Some of the key technologies driving the industry include:
- Building Information Modeling (BIM): BIM allows for the detailed planning and visualization of a building before construction begins. This technology helps to identify potential issues early in the design process, reducing the likelihood of delays and cost overruns.
- Automation and Robotics: The use of automation in manufacturing helps to improve the precision and efficiency of the prefabrication process. Robotics can be used to assemble complex components with a high degree of accuracy, ensuring that the final building meets exact specifications.
- 3D Printing: While still in its early stages, 3D printing has the potential to revolutionize prefabrication by allowing for the creation of complex building components on-site. This technology could further reduce construction times and costs in the future.
In Pakistan, the adoption of these technologies is helping to bring the construction industry in line with international best practices, making prefabrication an increasingly attractive option.
Challenges in Prefabricated Construction in Pakistan
Despite the many advantages of prefabricated multi-story buildings, there are also challenges that need to be addressed for wider adoption in Pakistan. Some of the common challenges include:
- Logistical Issues: Transporting large prefabricated components to the construction site can be challenging, particularly in areas with limited infrastructure. Solutions include developing better transportation networks and using smaller, more modular components that are easier to transport.
- Regulatory and Building Code Compliance: Ensuring that prefabricated buildings meet local building codes and regulations is critical to their success. In Pakistan, this requires close coordination with government agencies and adherence to national and international standards.
- Market Acceptance: While prefabrication is gaining popularity, there is still a perception that traditional construction methods are superior. Educating developers, architects, and the general public about the benefits of prefabrication is essential to overcoming this challenge.
By addressing these challenges, the prefabrication industry in Pakistan can continue to grow and contribute to the country’s development goals.
Regulations and Building Codes
Compliance with building codes and regulations is essential for the successful implementation of prefabricated multi-story buildings. In Pakistan, the regulatory framework for prefabrication is still evolving, but several key considerations must be taken into account:
- Building Codes: Prefabricated buildings must comply with national and local building codes, which govern aspects such as structural integrity, fire safety, and accessibility. In Pakistan, these codes are often based on international standards, but they may also include specific requirements for local conditions.
- Government Incentives: To promote the adoption of prefabrication, the Pakistani government has introduced various incentives, such as tax breaks and subsidies for green building practices. These incentives can help to offset the initial costs of prefabrication and make it a more attractive option for developers.
- Approval Processes: The approval process for prefabricated buildings can be streamlined through collaboration with government agencies. Early engagement with regulatory bodies can help to ensure that projects meet all necessary requirements and avoid delays.
By adhering to regulations and taking advantage of government incentives, developers can successfully implement prefabricated multi-story buildings in Pakistan.
Case Studies: Successful Prefabricated Multi-Story Projects
Several successful prefabricated multi-story projects in Pakistan demonstrate the potential of this construction method:
- Islamabad Residential Complex: This project involved the construction of a multi-story residential complex using modular prefabrication. The use of prefabrication allowed the project to be completed in record time, with significant cost savings compared to traditional construction methods.
- Lahore Commercial Building: A commercial building in Lahore was constructed using panelized prefabrication, resulting in a modern and energy-efficient structure. The project showcased the design flexibility of prefabrication, with a customized facade that met the client’s specific aesthetic requirements.
- Karachi Office Tower: This office tower in Karachi was built using hybrid prefabrication, combining modular and panelized elements. The project was completed ahead of schedule, highlighting the speed and efficiency of prefabrication.
These case studies provide valuable insights into the benefits of prefabricated construction and the lessons learned from implementing these projects in Pakistan.
Comparing Prefabrication to Traditional Construction
When comparing prefabrication to traditional construction methods, several key differences emerge:
- Cost: Prefabrication generally offers lower upfront costs and more predictable budgets due to the reduced likelihood of delays and cost overruns. Traditional construction can be more expensive due to labor costs and the potential for unforeseen issues.
- Speed: Prefabrication is significantly faster than traditional construction, as components are manufactured in parallel with site preparation. Traditional construction often takes longer due to the sequential nature of on-site work.
- Quality: The factory-controlled environment of prefabrication ensures consistent quality and adherence to standards. Traditional construction is more susceptible to variations in quality due to on-site conditions.
- Environmental Impact: Prefabrication generates less waste and is generally more energy-efficient than traditional construction. Traditional methods often result in higher levels of waste and energy consumption.
The choice between prefabrication and traditional construction depends on the specific needs of the project, including budget, timeline, and environmental considerations.
Future Trends in Prefabricated Construction in Pakistan
The future of prefabricated construction in Pakistan is bright, with several emerging trends expected to drive growth:
- Modular Construction: The use of modular construction techniques is expected to increase, allowing for greater flexibility and faster project completion times. This trend is particularly relevant for urban areas where space is limited and construction timelines are tight.
- Sustainable Building Practices: As environmental concerns continue to grow, the demand for sustainable building practices will drive the adoption of prefabrication. The use of green materials and energy-efficient designs will become increasingly important in the construction industry.
- Technological Advancements: Ongoing advancements in technology, such as the use of robotics and 3D printing, will further enhance the efficiency and quality of prefabricated buildings. These innovations will make prefabrication an even more attractive option for developers.
- Government Support: Continued government support in the form of incentives and regulatory frameworks will play a crucial role in promoting the adoption of prefabrication in Pakistan. This support will help to address some of the challenges facing the industry and encourage more developers to embrace this innovative construction method.
Overall, the future of prefabricated construction in Pakistan is promising, with the potential to transform the construction industry and contribute to the country’s development goals.
How to Choose the Right Prefabrication Partner
Choosing the right prefabrication partner is critical to the success of a project. Here are some key factors to consider:
- Experience: Look for a partner with a proven track record in prefabricated construction, particularly in multi-story buildings. Experience in the local market is also important, as it ensures that the partner is familiar with the specific challenges and regulations in Pakistan.
- Technological Capabilities: The use of advanced technologies, such as BIM and automation, is essential for ensuring the quality and efficiency of prefabricated buildings. Choose a partner that invests in these technologies and has the expertise to use them effectively.
- Project Portfolio: Review the partner’s portfolio of completed projects to assess their capabilities and the quality of their work. Look for examples of similar projects to the one you are planning, and consider visiting completed sites if possible.
- Reputation: Reputation is a key indicator of a partner’s reliability and professionalism. Seek out testimonials and reviews from previous clients, and ask for references if needed.
By carefully selecting a prefabrication partner that meets these criteria, developers can ensure that their project is completed on time, within budget, and to the highest standards of quality.
Steps to Planning a Prefabricated Multi-Story Building Project
Planning a prefabricated multi-story building project involves several key steps:
- Initial Concept and Feasibility Study: Begin by defining the project’s goals, budget, and timeline. Conduct a feasibility study to determine whether prefabrication is the right choice for the project, taking into account factors such as site conditions and regulatory requirements.
- Design and Engineering: Work with architects and engineers to develop detailed plans for the building. This phase includes the selection of materials, design of structural components, and planning for utilities and services. The use of BIM can streamline this process and ensure that all aspects of the project are carefully coordinated.
- Partner Selection: Choose a prefabrication partner based on the criteria outlined above. Engage with the partner early in the process to ensure that they are involved in the design and planning phases.
- Manufacturing and Assembly Planning: Coordinate with the prefabrication partner to plan the manufacturing and assembly process. This phase includes scheduling the production of components, arranging for transportation, and planning the on-site assembly.
- Permitting and Approvals: Obtain all necessary permits and approvals from local authorities. This may involve submitting detailed plans and specifications, as well as meeting specific regulatory requirements.
- Construction and Assembly: Once all preparations are complete, the construction and assembly phase can begin. This phase involves the transportation of prefabricated components to the site, assembly of the building, and completion of any remaining on-site work.
- Final Inspections and Handover: Conduct final inspections to ensure that the building meets all safety and quality standards. Once the building is approved, it can be handed over to the client or occupants.
By following these steps, developers can ensure a successful prefabricated multi-story building project that meets all requirements and expectations.
FAQs on Prefabricated Multi-Story Buildings in Pakistan
What are the main benefits of prefabricated multi-story buildings in Pakistan?
Prefabricated multi-story buildings offer cost savings, faster construction times, improved sustainability, and enhanced safety compared to traditional construction methods.
How do prefabricated buildings compare to traditional construction in terms of cost?
Prefabricated buildings are generally more cost-effective due to reduced labor costs, material efficiency, and faster project completion. They also offer more predictable costs and fewer budget overruns.
Are prefabricated buildings safe and durable?
Yes, prefabricated buildings are engineered to meet strict safety standards, with components manufactured under controlled conditions to ensure structural integrity and durability.
What materials are commonly used in prefabricated buildings?
Common materials include steel for structural frameworks, concrete for walls and floors, and wood for interior finishes. These materials are chosen for their strength, durability, and environmental impact.
How long does it take to construct a prefabricated multi-story building?
The construction time for a prefabricated multi-story building is typically much shorter than traditional construction, with some projects completed in a fraction of the time.
What is the environmental impact of prefabricated buildings?
Prefabricated buildings are environmentally friendly due to efficient material use, reduced waste, and energy-efficient designs. They contribute to lower carbon footprints and align with sustainable building practices.
Conclusion: The Growing Role of Prefabrication in Pakistan
The adoption of prefabricated multi-story buildings in Pakistan is playing a crucial role in addressing the country’s construction challenges, offering faster, more cost-effective, and sustainable solutions. As the industry continues to grow and innovate, prefabrication is set to become an increasingly important part of the construction landscape in Pakistan. By embracing this innovative approach, developers can meet the demands of rapid urbanization, contribute to environmental sustainability, and deliver high-quality buildings that stand the test of time.
This Post Has 0 Comments