AspectDetailsAffordabilityWarehouse rental in Karachi offers cost-effective options compared to owning a warehouse. Businesses can save…
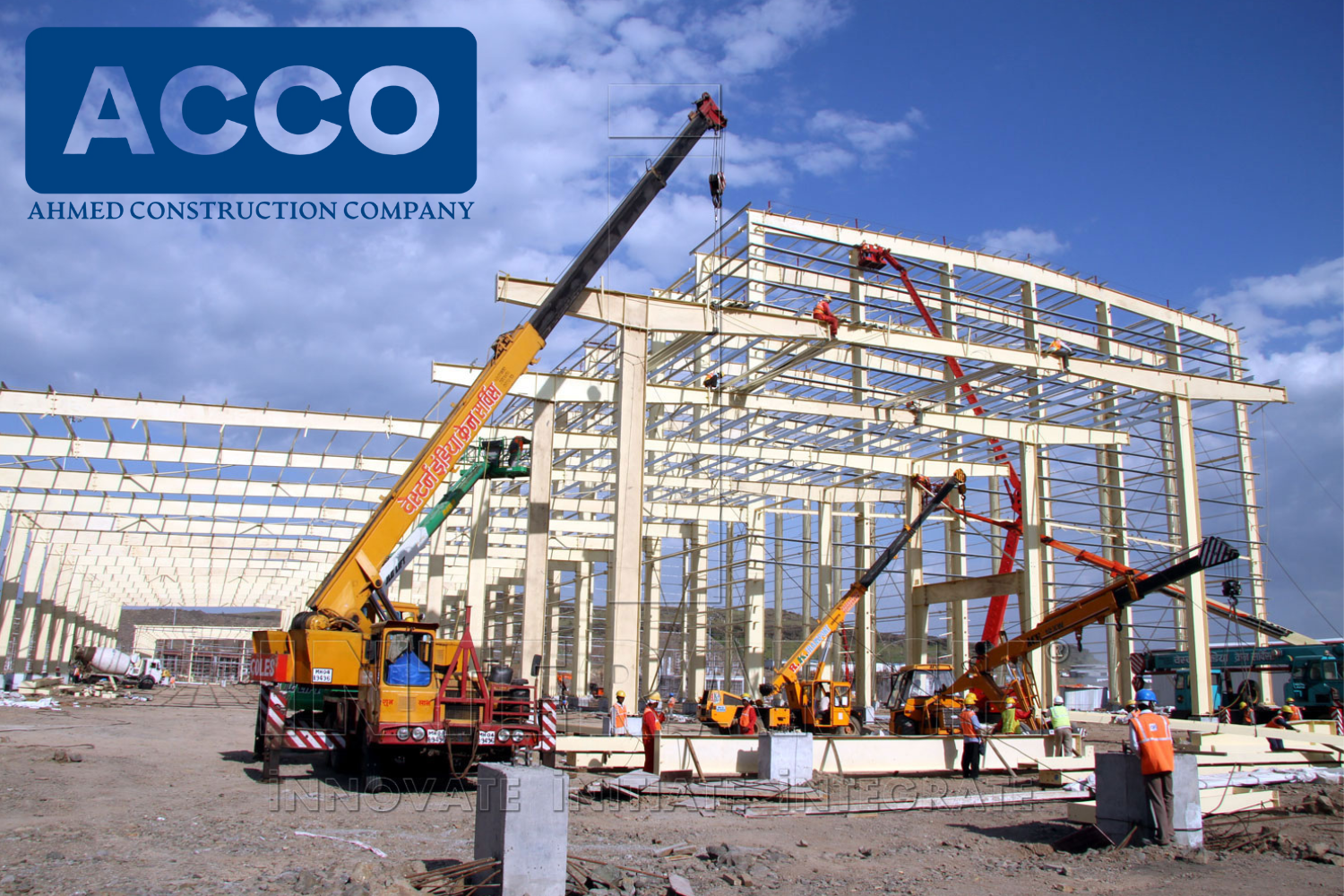
EPACK Understanding the Process of Pre Engineering Buildings in Pakistan
- Introduction
- Overview of Pre-Engineered Buildings (PEBs)
- Importance of PEBs in the Construction Industry
- What are Pre-Engineered Buildings?
- Definition and Key Characteristics
- Historical Background
- Benefits of Pre-Engineered Buildings
- Cost Efficiency
- Speed of Construction
- Design Flexibility
- Sustainability
- Steps in the Pre-Engineering Building Process
- Design and Planning
- Needs Assessment
- Conceptual Design
- Detailed Engineering
- Manufacturing
- Material Selection
- Fabrication of Components
- Logistics and Transportation
- Packaging and Shipping
- Site Preparation
- Construction and Assembly
- On-Site Assembly
- Quality Control
- Finishing and Handover
- Interior and Exterior Finishing
- Final Inspections
- Handover to Client
- Design and Planning
- Key Considerations in the PEB Process
- Selecting the Right Contractor
- Experience and Reputation
- Past Projects and References
- Compliance with Regulations
- Local Building Codes
- Environmental Regulations
- Project Management
- Timeline Management
- Budget Management
- Selecting the Right Contractor
- Case Studies of PEB Projects in Pakistan
- Industrial Facilities
- Commercial Complexes
- Residential Buildings
- Challenges and Solutions in the PEB Process
- Common Challenges
- Innovative Solutions
- Future of Pre-Engineered Buildings in Pakistan
- Technological Advancements
- Market Trends
- Conclusion
- Summary of Key Points
- Final Thoughts on the PEB Process
- FAQs
- What types of projects are best suited for PEBs?
- How long does the PEB process take from start to finish?
- What materials are commonly used in PEBs?
- Can PEBs be customized to specific needs?
- What are the maintenance requirements for PEBs?
Epack Understanding the Process of Pre Engineering Buildings in Pakistan
Introduction
Pre-Engineered Buildings (PEBs) are transforming the construction industry in Pakistan. Offering a blend of cost efficiency, rapid construction, and design flexibility, PEBs are increasingly becoming the go-to choice for various projects. Understanding the process behind these innovative structures is crucial for anyone considering investing in them.
What are Pre-Engineered Buildings?
Pre-Engineered Buildings (PEBs) are structures that are fabricated off-site and assembled on-site. They are designed to meet specific requirements and are known for their efficiency and versatility. Historically, PEBs have evolved from simple, utilitarian designs to complex structures capable of housing diverse functions.
Benefits of Pre-Engineered Buildings
Cost Efficiency: PEBs reduce overall construction costs through efficient use of materials and labor.
Speed of Construction: The prefabrication process allows for faster construction times compared to traditional methods.
Design Flexibility: PEBs can be customized to suit various architectural and functional needs.
Sustainability: PEBs often use sustainable materials and processes, reducing the environmental impact.
Steps in the Pre-Engineering Building Process
Design and Planning
Needs Assessment: Understanding the specific requirements of the project, including size, function, and budget.
Conceptual Design: Developing initial design concepts that meet the project’s requirements.
Detailed Engineering: Creating detailed drawings and specifications to guide the manufacturing and construction processes.
Manufacturing
Material Selection: Choosing high-quality materials that meet the project’s specifications and standards.
Fabrication of Components: Manufacturing the building components in a controlled factory environment to ensure precision and quality.
Logistics and Transportation
Packaging and Shipping: Safely packaging the prefabricated components and transporting them to the construction site.
Site Preparation: Preparing the construction site, including foundation work and infrastructure setup.
Construction and Assembly
On-Site Assembly: Assembling the prefabricated components on-site according to the detailed engineering plans.
Quality Control: Conducting inspections and tests to ensure that the assembly meets quality and safety standards.
Finishing and Handover
Interior and Exterior Finishing: Completing the interior and exterior finishes according to the project’s specifications.
Final Inspections: Performing final inspections to ensure the building is ready for occupancy.
Handover to Client: Officially handing over the completed building to the client.
Key Considerations in the PEB Process
Selecting the Right Contractor
Experience and Reputation: Choosing a contractor with a proven track record in PEB construction.
Past Projects and References: Reviewing previous projects and seeking references to assess the contractor’s capabilities.
Compliance with Regulations
Local Building Codes: Ensuring the design and construction comply with local building codes and regulations.
Environmental Regulations: Adhering to environmental regulations to minimize the project’s impact on the environment.
Project Management
Timeline Management: Establishing a realistic timeline and managing the project to stay on schedule.
Budget Management: Monitoring costs to ensure the project stays within budget.
Case Studies of PEB Projects in Pakistan
Industrial Facilities
Numerous industrial facilities in Pakistan have successfully utilized PEBs, benefiting from their cost efficiency and rapid construction times.
Commercial Complexes
Commercial complexes have also adopted PEBs, leveraging their flexibility in design and efficient use of space.
Residential Buildings
Residential projects, though less common, are beginning to see the advantages of PEBs, particularly in terms of cost and speed.
Challenges and Solutions in the PEB Process
Common Challenges
Challenges in the PEB process can include market perception, regulatory hurdles, and the availability of skilled labor.
Innovative Solutions
Solutions to these challenges involve raising awareness about PEB benefits, streamlining regulatory processes, and investing in training for skilled labor.
Future of Pre-Engineered Buildings in Pakistan
Technological Advancements
Ongoing technological advancements are enhancing the efficiency and capabilities of PEBs.
Market Trends
The market for PEBs in Pakistan is expected to grow, driven by the numerous benefits they offer.
Conclusion
The process of constructing Pre-Engineered Buildings involves several key steps, from design and planning to construction and finishing. Understanding these steps is essential for anyone considering a PEB project. With the right approach, PEBs offer a highly efficient and flexible solution for various building needs in Pakistan.
FAQs
What types of projects are best suited for PEBs? PEBs are ideal for industrial facilities, commercial complexes, and increasingly, residential buildings.
How long does the PEB process take from start to finish? The timeline can vary depending on the project’s size and complexity, but PEBs generally take less time to construct than traditional buildings.
What materials are commonly used in PEBs? Common materials include steel for the framework and various cladding and insulation materials for the building envelope.
Can PEBs be customized to specific needs? Yes, PEBs offer great flexibility in design and can be customized to meet specific requirements.
What are the maintenance requirements for PEBs? PEBs require minimal maintenance, focusing on regular inspections and minor repairs to ensure longevity.
This Post Has 0 Comments